Achieve a Flawless Finish: How to Choose the Right Surface Conditioning Discs
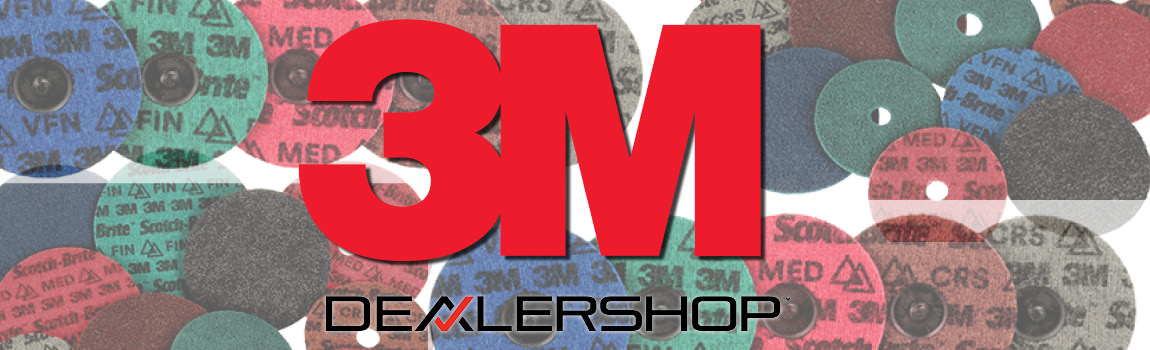
Are you tired of struggling to achieve a flawless finish on your projects? Look no further. In this article, we will guide you on how to choose the right surface conditioning discs to achieve impeccable results every time.
Finding the perfect surface conditioning discs can be a daunting task, with a myriad of options available in the market. But fear not! Our expert advice will help steer you in the right direction.
Whether you're working with wood, metal, or even concrete, selecting the appropriate surface conditioning discs can significantly impact the outcome of your project. From removing imperfections to creating a smooth and polished surface, these discs are an essential tool in any craftsman's arsenal.
Our in-depth guide will walk you through the various factors to consider when choosing surface conditioning discs, such as grit size, abrasiveness, and material compatibility. We'll also provide insights into different disc types and share tips on how to prolong their lifespan, making every dollar count.
Read on to discover the secrets of achieving a flawless finish with the right surface conditioning discs.
Why surface conditioning discs are important for achieving a flawless finish
Achieving a flawless finish on your projects is a top priority for any craftsman or DIY enthusiast. Surface conditioning discs play a vital role in this process by removing imperfections and creating a smooth surface that is ready for further finishing. These discs excel at removing rust, oxidation, paint, and other surface contaminants, ensuring that your workpiece is clean and prepped for the next stage.
One of the key advantages of using surface conditioning discs is their versatility. They can be used on a wide range of materials, including wood, metal, plastic, and even concrete. This makes them a valuable tool for various applications, from woodworking and metal fabrication to automotive restoration and home improvement.
Another reason why surface conditioning discs are essential for achieving a flawless finish is their ability to minimize heat buildup. Unlike traditional abrasives, which can generate excessive heat and cause damage to the workpiece, surface conditioning discs are designed to run cooler. This temperature control not only prolongs the life of the disc but also prevents heat-related issues such as discoloration and warping of the material.
3M Scotch-Brite 07485 No Hole Non-Woven Surface Conditioning Discs, 3 in Dia, Coarse Grade, Aluminum Oxide Abrasive, 25 Discs
The Scotch-Brite Roloc Surface Conditioning Disc combines our durable, non-woven disc with the efficient 3M Roloc quick-change attachment system for an effective disc that cleans, finishes, blends, and deburrs. Our non-woven fiber construction conforms well to help preserve irregular or contoured surfaces and the Roloc backing supports the disc for aggressive cutting.Types of surface conditioning discs
When it comes to surface conditioning discs, there are several types to choose from, each offering specific benefits for different applications. Let's explore some of the most common types:
1. Coated Abrasive Discs: These discs feature a layer of abrasive grains bonded to a backing material, such as cloth or paper. They are highly effective at removing material and are commonly used for heavy-duty applications. Coated abrasive discs come in various grits, allowing you to choose the level of aggressiveness required for your project.
Norton 66261131558 6" Coated Sanding Discs, 320 Grit, Extra Fine Grade, Aluminum Oxide Abrasive, Champagne, 100-Discs
Quickly attach the A275OP fine grit paper H&L disc to a random orbital sander or a right angle grinder by means of the convenient hook and loop back. The P-graded, heat-treated aluminum oxide abrasive provides fast cuts and reliable results, while the fiber-reinforced B-weight latex-saturated backing delivers 50 to 60% greater tear resistance without sacrificing flexibility. The water-based, non-pigmented stearate No-Fil coating ensures there's no color transfer to your workpiece, and the open coat design helps resist loading.2. Non-Woven Discs: Non-woven discs are made from nylon fibers that are bonded together and impregnated with abrasive grains. They are known for their flexibility and conformability, making them ideal for reaching intricate or curved surfaces. Non-woven discs are available in different densities, allowing you to choose between aggressive material removal or finer surface conditioning.
3. Surface Conditioning Discs with Grinding Aid: These discs are similar to non-woven discs but with the added benefit of a grinding aid. The grinding aid helps to reduce heat buildup and prevent loading, making these discs ideal for applications that generate a lot of heat, such as grinding and blending stainless steel.
4. Unitized Discs: Unitized discs are made by compressing layers of non-woven material together, creating a dense and durable disc. They are commonly used for deburring, blending, and polishing applications. Unitized discs are available in different densities, allowing you to choose between aggressive material removal or fine finishing.
Scotch-Brite 17184 No-Hole EXL Unitized Wheel, 3 in, 2S-Fine Grade, Silicon Carbide, Gray
Scotch-Brite Roloc EXL unitized wheel is strong and effective for edge deburring and finishing. Our wheel performs well in a variety of metal working applications and machined parts where close tolerances are important.5. Flap Discs: Flap discs combine the benefits of both grinding and sanding discs. They consist of overlapping flaps of abrasive material that are attached to a backing plate. Flap discs are highly versatile and can be used for both stock removal and finishing applications. They are particularly effective at blending and smoothing welds.
By understanding the different types of surface conditioning discs available, you can choose the one that best suits your specific project requirements.
Factors to consider when choosing surface conditioning discs
Selecting the right surface conditioning discs for your project can be a daunting task, given the wide range of options available in the market. However, by considering a few key factors, you can narrow down your choices and make an informed decision. Here are some factors to consider when choosing surface conditioning discs:
Grit size
The grit size of a surface conditioning disc determines its aggressiveness and the level of material removal it can achieve. Generally, lower grit numbers indicate a coarser abrasive, while higher grit numbers indicate a finer abrasive. For heavy material removal or rough surface conditioning, a lower grit disc may be suitable. For lighter material removal or fine finishing, a higher grit disc would be more appropriate. It's essential to choose the right grit size based on the nature of your project and the desired outcome.
Abrasiveness
Different surface conditioning discs have varying levels of abrasiveness, which affects their cutting power and material removal rate. Some discs are more aggressive and are designed for heavy-duty applications, while others are milder and are better suited for finer surface conditioning. Understanding the abrasiveness of a disc will help you select the right one for your project, ensuring optimal results without damaging the workpiece.
Material compatibility
Consider the material you are working with to ensure compatibility with the surface conditioning disc. Different materials require different abrasives and disc compositions for optimal performance. For example, when working with wood, a disc with aluminum oxide abrasive may be suitable, while when working with stainless steel, a disc with zirconia alumina abrasive may be more effective. Always check the manufacturer's recommendations and choose a disc that is specifically designed for the material you are working with.
Backing material
The backing material of a surface conditioning disc plays a crucial role in its durability and performance. Common backing materials include cloth, paper, polyester, and fiberglass. Each material has its own strengths and weaknesses. For example, cloth-backed discs are flexible and durable, making them suitable for heavy-duty applications. On the other hand, paper-backed discs are more economical and are better suited for lighter applications. Consider the demands of your project and choose a backing material that can withstand the required level of use and abuse.
Disc shape and size
Surface conditioning discs are available in various shapes and sizes to accommodate different applications and tools. The most common shapes include discs, wheels, and belts. Discs are versatile and can be used on handheld tools or bench grinders. Wheels are suitable for larger surface areas and are typically used on stationary machines. Belts are commonly used for sanding and blending applications on flat or curved surfaces. Consider the nature of your project and choose the appropriate disc shape and size for optimal results.
By taking into account these factors, you can confidently select the right surface conditioning discs that will deliver the desired results for your project.
How to determine the right grit for your application
Determining the right grit size for your application is crucial for achieving the desired level of material removal and surface conditioning. The grit size you choose will depend on the initial condition of the workpiece and the desired outcome. Here are some general guidelines to help you determine the right grit size:
1. Coarse grits (40-60): Coarse grits are suitable for heavy material removal, such as rust or paint removal, or when starting with a rough or uneven surface. They are also ideal for shaping or leveling surfaces.
2. Medium grits (80-120): Medium grits are commonly used for general surface conditioning and blending applications. They are effective at removing scratches, burrs, and minor imperfections, leaving a smooth and even finish.
3. Fine grits (180-240): Fine grits are used for finer surface conditioning, such as preparing surfaces for painting or staining. They are also suitable for light deburring or polishing applications.
4. Very fine grits (320-600): Very fine grits are used for achieving a smooth and polished finish. They are ideal for final finishing touches or when working with delicate materials that require minimal material removal.
It's important to note that these are general guidelines, and the appropriate grit size may vary depending on the specific requirements of your project. Always test the disc on a small, inconspicuous area before proceeding with the entire workpiece.
Choosing the right backing material for your surface conditioning disc
The backing material of a surface conditioning disc plays a critical role in its durability, flexibility, and performance. Different backing materials offer varying levels of strength, tear resistance, and flexibility. Here are some common backing materials and their characteristics:
1. Cloth: Cloth-backed surface conditioning discs are known for their durability and flexibility. They are ideal for heavy-duty applications and can withstand high-pressure grinding or blending. Cloth-backed discs are tear-resistant and have a longer lifespan compared to other backing materials.
2. Paper: Paper-backed surface conditioning discs are economical and are suitable for lighter applications. They are commonly used for finer surface conditioning or when cost is a factor. Paper-backed discs are less tear-resistant than cloth-backed discs but offer good flexibility.
3. Polyester: Polyester-backed surface conditioning discs are a middle-ground option, offering a balance between durability and flexibility. They are suitable for a wide range of applications and provide good performance and longevity.
4. Fiberglass: Fiberglass-backed surface conditioning discs are rigid and provide excellent support for heavy-duty applications. They are highly resistant to tearing and can withstand high-pressure grinding. Fiberglass-backed discs are commonly used for stock removal or applications that require aggressive material removal.
Consider the demands of your project and choose a backing material that can withstand the required level of use and abuse while providing the necessary flexibility for optimal performance.
Different disc shapes and sizes for different applications
Surface conditioning discs come in various shapes and sizes to accommodate different applications and tools. The choice of disc shape and size will depend on the nature of your project and the tools you have at your disposal. Here are some common disc shapes and their typical applications:
1. Flat discs: Flat discs are the most versatile shape and can be used on handheld tools or bench grinders. They are suitable for a wide range of applications, from surface conditioning and deburring to blending and polishing.
2. Flap discs: Flap discs consist of overlapping flaps of abrasive material that are attached to a backing plate. They are highly versatile and can be used for both stock removal and finishing applications. Flap discs are particularly effective at blending and smoothing welds.
3. Roloc discs: Roloc discs feature a twist-on/off fastening system, allowing for quick and easy disc changes. They are commonly used with rotary tools and are ideal for applications that require frequent disc swapping or access to hard-to-reach areas.
4. Strip discs: Strip discs are designed for aggressive material removal, such as paint or rust removal. They feature a radial bristle design that provides a high level of cutting power. Strip discs are commonly used in automotive restoration, metal fabrication, and surface preparation.
Consider the specific requirements of your project and choose the disc shape and size that will allow you to achieve the desired results efficiently and effectively.
Proper usage and maintenance of surface conditioning discs
To ensure optimal performance and longevity of your surface conditioning discs, it's essential to follow proper usage and maintenance guidelines. Here are some tips to help you get the most out of your discs:
1. Use the right technique: Always use the recommended technique for the specific application you are working on. This includes the speed, pressure, and angle at which you operate the disc. Using the wrong technique can lead to poor results or premature disc wear.
2. Keep the disc clean: Surface conditioning discs can become clogged with debris, reducing their effectiveness. Regularly clean the discs by using a cleaning stick or brush to remove any buildup. This will help maintain consistent performance and prolong the life of the disc.
3. Store discs properly: When not in use, store your surface conditioning discs in a clean and dry environment. Avoid exposing them to extreme temperatures or moisture, as this can affect their performance and lifespan.
4. Inspect discs before use: Before using a surface conditioning disc, inspect it for any signs of damage or wear. Discard any discs that are cracked, torn, or have worn-out abrasive grains. Using damaged discs can result in poor performance and potential safety hazards.
5. Use appropriate safety gear: When using surface conditioning discs, always wear the appropriate safety gear, including safety glasses, gloves, and a dust mask. This will protect you from flying debris, dust, and potential injury.
By following these usage and maintenance tips, you can maximize the lifespan and performance of your surface conditioning discs, ensuring consistent and reliable results.
Where to buy high-quality surface conditioning discs
When it comes to purchasing surface conditioning discs, it's crucial to buy from reputable suppliers that offer high-quality products. Here are some sources where you can find reliable surface conditioning discs:
1. Specialty tool stores: Specialty tool stores often carry a wide range of surface conditioning discs, catering to various applications and requirements. These stores typically have knowledgeable staff who can assist you in selecting the right discs for your project.
2. Online marketplaces: Online marketplaces such as DealerShop offer a vast selection of surface conditioning discs. Reading customer reviews and ratings can help you gauge the quality and performance of the discs before making a purchase.
3. Manufacturer websites: Many manufacturers of surface conditioning discs have their own websites where you can find detailed product information, specifications, and purchasing options. Buying directly from the manufacturer ensures that you are getting genuine and high-quality products.
4. Local hardware stores: Local hardware stores often carry a selection of surface conditioning discs, catering to common applications. While the range may be more limited compared to specialty stores or online marketplaces, they can still be a convenient option for quick purchases.
When purchasing surface conditioning discs, it's important to consider factors such as quality, performance, and price. Look for reputable brands that offer a good balance between these factors, ensuring that you get the best value for your money.
Conclusion: Achieving a flawless finish with the right surface conditioning discs
Choosing the right surface conditioning discs is essential for achieving a flawless finish on your projects. These versatile tools can remove imperfections, smooth rough surfaces, and prepare materials for further finishing. By understanding the various types of surface conditioning discs, factors to consider when choosing them, and proper usage and maintenance techniques, you can optimize your results and prolong the lifespan of your discs.
Remember to consider factors such as grit size, abrasiveness, material compatibility, backing material, disc shape and size, and safety precautions when selecting and using surface conditioning discs.
Become a Member of DealerShop to learn more!
![]() | Email this Page |
![]() | Print this Page |
![]() | Share |